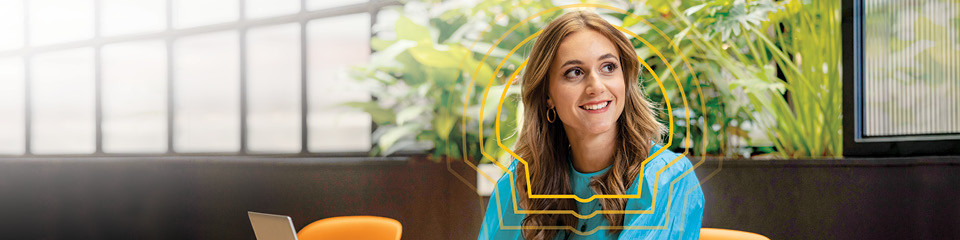
Make a difference
Do you like helping people? Do you like to make people smile? Are you passionate about putting people in a better place? Then you may have what it takes to join our amazing team?
What's the role -
Provide rotating equipment support on general purpose and large turbomachinery in a production unit team and during maintenance activities. In addition, provide quality assurance that the maintenance efforts related to overhauling the major rotating equipment meets the expected high standards for excellence. Finally, play a key role in the training of the maintenance staff in the specialized rotating equipment field.
Scope and responsibilities
Assist the rotating equipment engineers in identifying repetitive problems and turnaround cycle limiting issues with respect to the turbomachinery equipment and implement solutions to extend service life.
Maintain an awareness of outside machine shop capabilities, conduct shop audits with Shell's principle technical engineers, and provide inspection/expediting support on outside shop repairs.
Assist in the planning, preparation, and execution of repairs on major machinery trains including scope development and selection of maintenance crafts on shutdowns.
Document repairs on mechanical equipment and communicate reports to appropriate individuals in the organization.
Lead and/or participate in structured analysis processes such as root cause analysis (RCA), 5 causal reasoning questions (CRQ), Bad Actors Elimination, Risk Assessments, and Solution Development. Conduct failure analysis and problem solving of major rotating equipment problems. These issues are often initially identified as machinery problems but may involve complex systems evaluations.
Leverage Proactive Technical Monitoring (PTM) driven by "Find Small-Fix Small" mindset. Expand upon and apply existing PdM platforms such as vibration monitoring, compressor performance monitoring, lube oil condition monitoring, infrared thermography and Operator Task Management (OTM) to identify, analyze, predict and solve.
Serve as a "champion" for strict adherence to the Reliability Centered Maintenance (RCM) process by actively participating in RCM Studies, RCM Living Program Reviews and seeking other opportunities to build a more robust program.
Associated tasks:
Determine repair techniques for damaged equipment/parts for large repairs.
Evaluate manufacturer recommendations.
Check material compatibility vs. service and recommend alternatives.
Reference to Shell and location specifications and repair standards.
Give input on what is required for repair.
Find out what other locations are doing. Keep abreast of the "state of the art" technology.
Recommend tolerances and fits.
Test new techniques/materials.
Provide close technical supervision to repair process
Document major equipment repairs and communicate appropriate reports to the Production team and other stakeholders
Maintain/update turbomachinery paper and electronic files.
Be familiar with vibration data and Bently Nevada instrumentation on large rotating equipment.
Audit outside machine shop repair capabilities and provide feedback to Purchasing.
Review/adjust spare parts stock levels. This includes preparing Stock Request forms and updating SAP.
Expedite/Inspect repairs at outside machine shops.
Witness run-out readings, tolerance checks, balance runs, etc.
Witness NDT checks.
Communicate Shell's expectations on tolerances, standards, timing, costs, etc.
Review and approve scope of repairs as warranted.
Verify applicable API codes and Shell standards are being followed
Audit warehouse spare parts preservation and review and follow-up with Purchasing periodically.
Interface with the turnaround rotating equipment planner to plan, prepare, and execute repairs for major machinery on shutdowns.
Prepare a work list detailing the work to be done.
Prepare a tool list detailing the tools that will be needed.
Procure support from manufacturer on major machinery overhauls.
Provide technical support to the technicians doing the actual work.
Prepare detailed shutdown report.
Hold and attend critical meetings.
Update overhaul procedures.
Provide assistance to other Shell locations for projects and shutdowns.
Perform periodic unit inspections.
Safety items
Check oil mist system
Seal leaks
Unusual noises
Proper oil levels
Major compressor operating parameters
Problem equipment operation
Participate in goal setting and review.
Support troubleshooting of process problems which impact rotating machinery.
Monitor rotating equipment performance and investigate possible efficiency modifications for possible improvement.
Provide both formal and informal training for the Production Team Support Engineers, Rotating Equipment Engineers, and Maintenance Coordinators.
Participate in the development/review of plant procedures.
Coordinate and audit field repair contractors.
Selection
Writing contracts
Orientation
Supervise field activities
Attend required and developmental training.
HSSE
Corporate
Symposiums
Discipline Specific
Generate SAP work tickets to address rotating equipment issues.
Work tickets for equipment identified in distress by the vibration program
Work ticket to order materials
Skills & Requirements
What we need from you -
Must have legal authorization to work in the US on a full-time basis.
Required minimum 10 years of field experience supporting major turbomachinery
Knowledge in the application of rotating equipment performance and condition monitoring methods for large turbomachinery.
Skilled in the application of rotating equipment troubleshooting and reliability improvement process.
Hands on experience in the troubleshooting and repair of reciprocating and centrifugal compressors, steam turbine drivers, electrical motor drivers, single stage and multi-stage centrifugal pumps, canned motor pumps, positive displacement plunger and injection pumps, gearboxes, air cooler exchanger fans, furnace and boiler blowers, and conveyors.
Highly effective people skills with demonstrated ability to work on teams and with diverse workgroups including craft-persons, vendors, and various engineering disciplines.
The base salary range for this position is $101,000 - $151,000 per year. Individual pay will be based on various factors, such as relevant work experience, education, certifications, skill level, seniority, and internal equity.
For regular full-time or regular part-time employees of the Company (participating companies as listed in the Summary Plan Description), insurance coverage options include medical, dental, vision coverage, life Insurance, Business Travel Accident Insurance, and Occupational Accidental Death Benefit programs. Employees also participate in a company pension plan and a 401(k) plan. Paid leave includes up to 3 weeks of paid vacation time, up to 11 paid holidays, and parental leave offering 16 weeks of paid leave to birthing mothers, and 8 weeks of paid leave for non-birthing parents.
Additionally, employees are eligible for disability leave for up to 52 weeks at 100% or 50% of base pay. Shell also offers other compensation such financial reimbursement for adoption, wellness, education, and personal learning expenses, and some roles are eligible for discretionary long-term incentives. For interns, eligible benefits include medical, dental, and vision coverage, life insurance, Business Travel Accident Insurance, and Occupational Accidental Death Benefit programs; participation in a 401(k) plan; and paid leave for up to 11 paid holidays. Additional information on Shell's US benefit programs can be found at https://www.shell.us/careers/about-careers-at-shell/rewards-and-benefits.html
Company description
Shell is a global group of energy and petrochemical companies with about 84,000 employees across more than 70 countries. We aim to meet the world's growing need for more and cleaner energy solutions in ways that are economically, environmentally, and socially responsible. We have expertise in exploration, production, refining and marketing of oil and natural gas, and the manufacturing and marketing of chemicals.
As a global energy company operating in a challenging world, we set high standards of performance and ethical behaviors. We are judged by how we act and how we live up to our core values of honesty, integrity, and respect for people. Our Business Principles are based on these. They promote trust, openness, teamwork, and professionalism, as well as pride in what we do and how we conduct business.
Building on our core values, we aspire to sustain a diverse and inclusive culture where everyone feels respected and valued, from our employees to our customers and partners. A diverse workforce and an inclusive work environment are vital to our success, leading to greater innovation and better energy solutions.
An innovative place to work
There's never been a more exciting time to work at Shell. Everyone here is helping solve one of the biggest challenges facing the world today: bringing the benefits of energy to everyone on the planet, while managing the risks of climate change.
Join us and you'll add your talent and imagination to a business with the power to shape the future - whether by investing in renewables, exploring new ways to store energy or developing technology that helps the world to use energy more efficiently.
An inclusive place to work
To power progress together, we need to attract and develop the brightest minds and make sure every voice is heard. Here are just some of the ways we're nurturing an inclusive environment - one where you can express your ideas, extend your skills and reach your potential...
We're creating a space where people with disabilities can excel through a transparent recruitment process, workplace adjustments and ongoing support in their roles. Feel free to let us know about your circumstances when you apply, and we'll take it from there.
We're closing the gender gap - whether that's through action on equal pay or by enabling more women to reach senior roles in engineering and technology.
We're striving to be a pioneer of an inclusive and diverse workplace, promoting equality for employees regardless of sexual orientation or gender identity.
We consider ourselves a flexible employer and want to support you in finding the right balance. We encourage you to discuss this with us in your application.
A rewarding place to work
Combine our creative, collaborative environment and global operations with an impressive range of benefits and joining Shell becomes an inspired career choice.
We're huge advocates for career development. We'll encourage you to try new roles and experience new settings. By pushing people to reach their potential, we frequently help them find skills they never knew they had, or make career moves they never thought possible.
Disclaimer
Please note: We occasionally amend or withdraw Shell jobs and reserve the right to do so at any time, including prior to the advertised closing date.
Before applying, you are advised to read our data protection policy. This policy describes the processing that may be associated with your personal data and informs you that your personal data may be transferred to Royal Dutch/Shell Group companies around the world.
The Shell Group and its approved recruitment consultants will never ask you for a fee to process or consider your application for a career with Shell. Anyone who demands such a fee is not an authorized Shell representative and you are strongly advised to refuse any such demand.
Shell is an Equal Opportunity Employer.
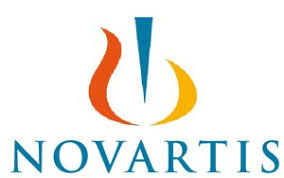
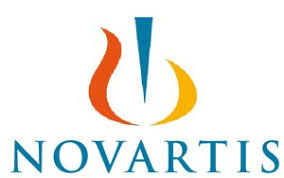
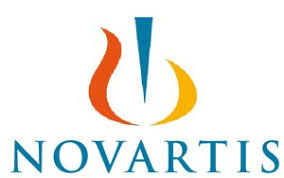