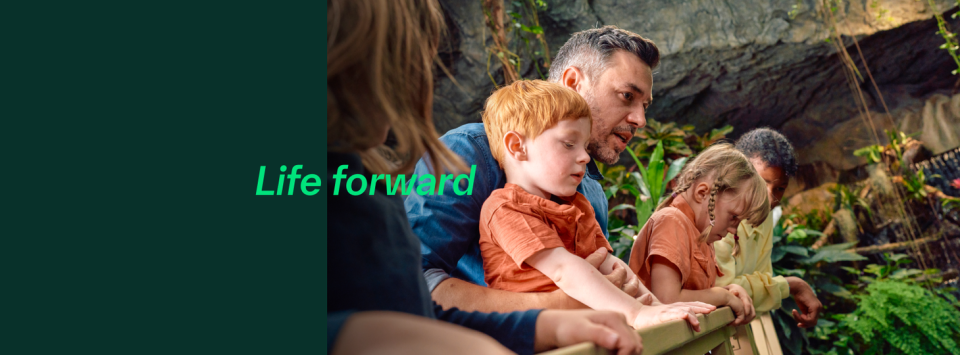
Description
As an employee of Boehringer Ingelheim, you will actively contribute to the discovery, development, and delivery of our products to our patients and customers. Our global presence provides opportunity for all employees to collaborate internationally, offering visibility and opportunity to directly contribute to the companies' success. We realize that our strength and competitive advantage lie with our people. We support our employees in several ways to foster a healthy working environment, meaningful work, diversity and inclusion, mobility, networking, and work-life balance. Our competitive compensation and benefit programs reflect Boehringer Ingelheim's high regard for our employees.
The Specialist, Operations Maintenance will provide mechanical technical and hands-on maintenance support to Boehringer Ingelheim process/production operations with primary focus on fermentation, anaerobe, aerobe, and virus production operations. This role will provide technical troubleshooting as well as training in the setup and operation of production and utility equipment including all aspects of mechanical systems such as fermenters, bioreactors, tanks, agitators, pumps, downstream processing, compressors, water, and steam systems as well as basic electrical troubleshooting and maintenance support of instruments, controls, robots, vision, manipulating and production handling equipment. The incumbent will become the Subject Matter Expert for maintaining equipment in assigned bldg. / area, providing guidance and input for field engineers.
Duties & Responsibilities
- With limited or no oversight from supervisor, maintains production process equipment supporting production schedules and quality requirements, may include additional operations equipment.
- Identifies and proposes improvement opportunities, including researching and calculating realized cost savings.
- Coordinates with Planner/Scheduler and supervisors to ensure that adequate scheduling information is communicated and that work orders are completed within compliance windows.
- Participates in deviation investigations and Go Sees, collaborating with quality and GFE compliance teams to provide viable solutions for CAPAs.
- Responsible for Preventative Maintenance (PM) creation and revisions for new and existing equipment to include parts, job plans, and LOTO.
- Interacts with external vendors to ensure end of life cycle components are identified and coordinates a phase out plan to maintain reliability of the equipment.
- Manages small projects and support engineering projects involving electro-mechanical applications relative to all facets of design, scope, performance parameters, testing and implementation.
- Prepares and provides status updates for GFE leadership and Senior Leadership team as needed.
- Participates in and responds to regulatory inspections as needed.
- Researches and calculates cost savings realized from improvement initiatives.
- Responsible for decision making when it comes to troubleshooting, adjustment, and repair of the equipment to achieve maximum performance.
- Coordinates with Engineering, Quality, Filling, and outside vendors to ensure reliability and mechanical readiness of the production systems.
- Accountable for creation thru close out of change controls and / or CAPA documentation as assigned in the electronic quality system.
- Documentation includes P&ID drawings, functional specifications, detailed design specifications, Turn-over-packages, material specifications, and other documentation as required.
- Works with engineering, maintenance and EHS personnel to develop appropriate engineering specifications, training, standard operating procedures, and preventative maintenance tasks for all new and existing production equipment.
- Provides necessary review and oversight when installing, repairing, or investigating equipment associated with the production equipment and systems (including contractors) to ensure proper execution and quality services.
Requirements
- High school diploma required; Technical institute training and certification in mechanical manufacturing applications fields preferred.
- Seven (7) years Mechanical maintenance & electrical experience in equipment common to biological, pharmaceutical or food processing.
- Supervisory or crew/job project leadership experience preferred.
- Familiarity with other facets of bio-pharmaceutical production processes and equipment including fermentation, bioreactor, autoclaves, pure steam, WFI and associated biological production process equipment/systems.
- Must be able to lift 50 pounds occasionally.
- Entry into Medical Surveillance Program (post hire).
- Ability to work in confined spaces.
- GMP gowning.
- Interpret PI&D drawings/schematics.
- Trace electrical circuits, follow diagrams, and conduct tests with circuit testers and other equipment.
- Knowledge (experience) of various computer programs including Microsoft Office programs, and various maintenance databases.
- Hydraulic experience preferred.
- Utilization of good people and communication skills (verbal and written).
- Experience working in team-oriented atmosphere.
- Project management skills preferred.
- Multitasking, time management, prioritization, and self-starting skills desired.
- High level of quality of work, attention to details, compliance to established procedures.
- High level of technical knowledge relating to production equipment and experience with control or management of compliance related documentation.
Eligibility Requirements:
- Must be legally authorized to work in the United States without restriction.
- Must be willing to take a drug test and post-offer physical (if required).
- Must be 18 years of age or older.
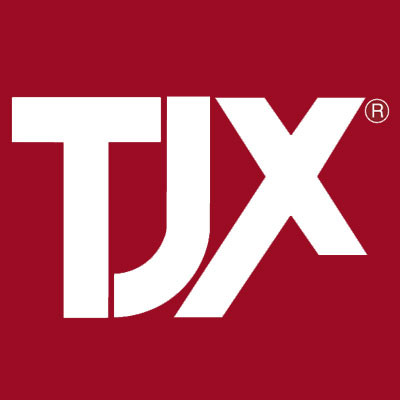
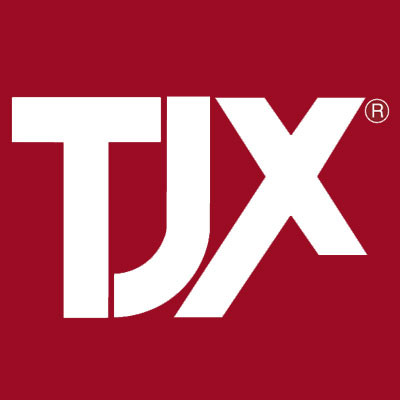
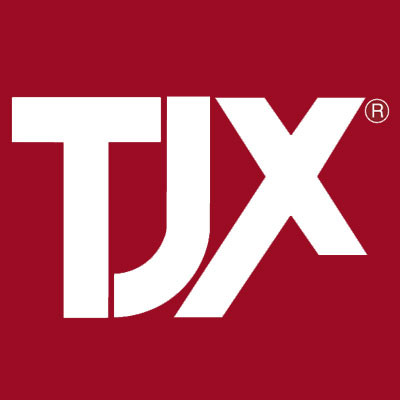